Битумно-полимерные мастики
Устройство бесшовной гидроизоляции (обмазочной) с применением битумно-латексной эмульсии Flexigum, битумно-полимерных мастик Mastigum Speed, Flexigum Paste
Технологии, так называемой, бесшовной напыляемой, обмазочной, жидкой гидроизоляции (жидкой резины) представляет собой антикоррозийное покрытие, выполняющие функцию гидроизоляции строительных конструкций, фундаментов зданий. Такое покрытие позволяет надежно изолировать труднодоступные участки основания, со сложной геометрией, где использование рулонных материалов неэффективно.
Flexigum — представляет собой двухкомпонентный гидроизоляционный материал, состоящий из битумно-латексной эмульсии с высоким содержанием синтетического латекса на основе полихлоропренового каучука и коагулянта.
Mastigum Speed — это двухкомпонентная мастика, состоящая из битумно-латексной эмульсии и цементно-полимерной пудры.
Flexigum Paste — это однокомпонентная мастика, состоящая из полимерного битума, модифицированного латексом
Все вышеуказанные материалы вне зависимости от способа нанесения создают на поверхности целостное покрытие, без швов, материалы отлично заполняют все трещины, швы, и поры обрабатываемой поверхности, обеспечивая тем самым идеальную защиту от воды, пара и любой другой агрессивной жидкости.
Битумно-латексная
эмульсия
Flexigum
Двухкомпонентная эластичная битумная мастика
Mastigum Speed
Нанесение битумно-латексной эмульсии Flexigum осуществляется только методом безвоздушного напыления, а материалы Mastigum Speed и Flexigum Paste можно наносить валиком и кистью. Все материалы характеризуются холодным нанесением и моментальным застыванием.
Качество гидроизоляционного покрытия, полученного на основе Flexigum, Mastigum Speed, Flexigum Paste, превосходит многие известные нам отечественные и зарубежные аналоги — вода практически не проникает сквозь полимер к фундаменту или стенам подвала. Наносить материал можно с легкостью на любые поверхности, при этом плоскости их расположения значения не имеют, будь они вертикальными, горизонтальными или наклонными.
Для одноразового использования покупать или арендовать дорогостоящую установку экономически не выгодно. Поэтому при самостоятельном ведении гидроизоляционных работ на фундаменте целесообразно использовать двухкомпонентную битумную мастику Mastigum Speed или битумно-полимерную мастику Flexigum Paste, которые можно наносить валиком или кистью. Любой метод нанесения эмульсии или мастики на поверхность конструкции предполагает получение бесшовного монолитного покрытия.
При гидроизоляции ручным способом толщина слоя покрытия и расход мастики будут несколько выше, чем при напылении (примерно на 5-10%). Поэтому, планируя обработку значительных площадей поверхности, необходимо учитывать экономическую выгоду при выборе того или иного способа нанесения материала.
Не подлежит сомнению тот факт, что качество гидроизоляции, выполненной механизированным способом, будет выше. Это связано с тем, что эмульсия, подаваемая под давлением из установки на поверхность фундамента, глубже проникает в ее поры, чем при нанесении валиком. При этом снижается расход материала и обеспечивается его максимальная адгезия. Кроме того, напылением всю процедуру гидроизоляции можно завершить за один день.
Преимущества технологии напыления (нанесения) бесшовной гидроизоляции.
Учитывая то, что оптимальная толщина покрытия составляет 3-4 мм, его эксплуатационные параметры эквивалентны аналогичным показателям рубероида, наклеенного на фундамент в несколько слоев. При этом отсутствует необходимость в герметизации швов между полотнами рулонного материала, так как полученная мембрана является полностью монолитной.
Помимо этого, выделяют такие преимущества Flexigum, MastigumSpeed, FlexigumPaste, которые в свою очередь и являются основными преимуществами перед другими гидроизоляционными материалами. :
- Долговечность до 75 лет – сохранение первоначальных характеристик на протяжении всего срока эксплуатации;
- Со временем покрытие становится более прочным и твердым, не теряя при этом эластичность;
- Характеризуется легкостью ремонта и восстановления;
- Отсутствие отслаивания от основания под воздействием неблагоприятных природных явлений;
- Температура эксплуатации в диапазоне от -50 до +100 градусов, при сильном нагревании битумно-полимерная изоляция плавится, но не горит.
- Благодаря отличной адгезии покрытия к бетону и другим основаниям, на резиновую гидроизоляцию фундамента можно клеить любой утеплитель или облицовку.
- Высокая степень эластичности покрытия (Mastigum Speed- 1000%, Flexigum-1900%) при различной температуре способствует его сохранности даже при значительной усадке фундамента в первые годы после постройки дома.
- Полное отсутствие швов – абсолютная монолитность, что выгодно отличает ее от рулонных материалов, применяемых для аналогичных целей.
- Водостойкость и непроницаемость покрытия исключает проникновение через него даже влаги, находящейся в парообразном состоянии.
- Полимерно-битумное покрытие с латексом в составе прочнее рубероида и тверже его, оно отлично сопротивляется разрыву, устойчиво к кислотам и воздействию микроорганизмов.
- Нанесение Flexigum на основание с помощью установки высокого давления имеет высокую производительность, которая выражается в изготовлении до 1000 м
- Эмульсии и мастики безопасны для окружающей среды и не токсичны.
Недостатками использования бесшовной гидроизоляции с применением Flexigum, Mastigum Speed, Flexigum Paste можно назвать более высокую стоимость материала по сравнению с рубероидом и наличие высокой квалификации исполнителя при работе с установкой для напыления эмульсии. Несмотря на эти минусы, совершенно очевидно, что старые методы гидроизоляции фундамента явно уступают данной технологии нанесения по большинству основных показателей: эластичности покрытия, его надежности, монолитности, герметичности и т.
Подготовка к бесшовной гидроизоляции фундамента.
Подготовительные работы являются неотъемлемым этапом гидроизоляции фундамента. Если здание уже находится в эксплуатации, его подземную часть перед проведением данной процедуры потребуется освободить от грунта, после чего внимательно осмотреть.
Земляные работы на данном этапе заключаются в выкопке траншеи, прилегающей к стенам фундамента по всему его периметру. Ширина должна быть такой, чтобы в ней было удобно работать — примерно 0,7-1 м. Ее глубина должна достигать подошвы фундамента.
Чтобы освободить доступ к порам материала фундамента, его стены желательно обработать с помощью пескоструйного аппарата, который позволяет выполнять дополнительную очистку конструкций путем подачи на их поверхности сыпучего абразива под давлением воздуха до 10 атмосфер.
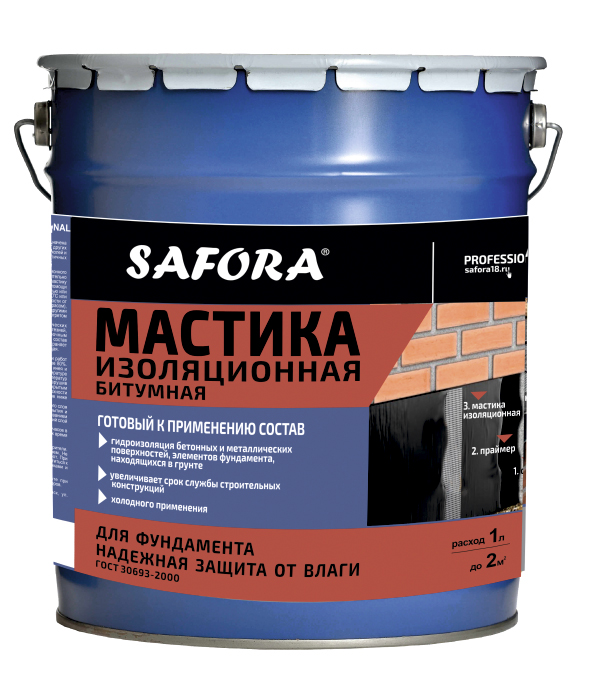
После этого очищенные стены фундамента следует отремонтировать путем заделки трещин и выбоин на их поверхности цементным раствором, а затем при необходимости покрыть соответствующей грунтовкой для повышения адгезии покрытия с основой. Если в основании фундамента проложена дренажная система, ее нужно осмотреть на предмет целостности, а при необходимости починить или заменить.
Подготовка к гидроизоляции старого фундамента требует немало сил, времени и даже денежных средств. Поэтому выполнять любые защитные покрытия на подземной части здания лучше в период его возведения. Это позволит избежать выполнения дополнительных земляных работ и перечисленных проблем, связанных с ними.

Технология нанесения бесшовной гидроизоляции на фундамент.
Независимо от способа нанесения жидкой гидроизоляции на фундамент, работать с ней в дождь или снег категорически не рекомендуется.
Обработку фундамента эмульсией ручным способом необходимо выполнять в несколько слоев до получения нужной толщины гидроизоляционного покрытия. Механизированный способ предполагает нанесение материала одним слоем. В любом случае толщина защитного покрытия не должна быть менее 2 мм. При заложении фундамента на глубину до 10 м слой его гидроизоляции должен составлять по толщине 3-4 мм, свыше 10 м соответственно — 5-6 мм. Для покрытия толщиной 4 мм потребуется в среднем 7кг/м2 битумно-латексной эмульсии Flexigum.
К началу выполнения гидроизоляционных работ прочность бетона на сжатие должна быть не менее 80% марочной прочности.
Для обеспечения отвода и быстрого высыхания влаги, которая выделяется в виде отдельных капель воды диаметром 1-5 мм из гидроизоляционной мембраны Flexigum, нанесение следует начинать с наиболее низкого участка, двигаясь к высокому.
Процесс напыления Flexigum осуществляется посредством подачи двух компонентов: битумно-латексной эмульсии и коагулянта (водного раствора СаCl), предназначенным для повышения скорости полимеризации материала. Жидкости подаются по двум контурам включающих систему гибких шлангов, которые соединены с двухсопельным распылителем, в соплах которого установлены конусовидные форсунки.
На выходе из распылителя две струи компонентов материала смешиваются в воздушной среде. Во время этого процесса происходит быстрое разрушение оболочки эмульгатора, а освобожденные частицы битума и латекса, попадая на поверхность основы, образуют мембрану. После отделения технологической влаги материал приобретает свойства и физико-механические показатели качественной бесшовной гидроизоляции. Проектный слой до 4мм напыляется на поверхность одним заходом.
При нанесении Mastigum Speed два компонента (А и Б) смешиваются с помощью электродрели в течение 2-х минут до образования однородной массы, после чего приготовленную смесь следует употребить (нанести на поверхность) в течение 60 минут с момента замешивания минимум 2-мя слоями.
Flexigum Paste — однокомпонентный гидроизоляционный материал, который наносится в 2-3 слоя кистью или валиком, в результате чего формируется мембрана аналогичная мембране Flexigum.
Качество сцепления гидроизоляционной мембраны с поверхностью проверяется через 24 часа путем контрольных надрезов ножом. Площадь мембраны, которая отрывается, при нормативном сцеплении с бетоном не должна превышать 2 см2.
В итоге хочется сказать следующее. В любом случае достоинств у битумно-полимерных материалов, модифицированных латексом, гораздо больше, чем недостатков. Более длительным сроком службы и более надежной защитой от влаги обладают мембраны, полученные в результате применения двухкомпонентных эмульсий и мастик.
Назад
Мастика битумно-полимерная МБП
Мастика изготавливается из высококачественных битумов, органических растворителей, минерального наполнителя, пластификатора, натурального и синтетических каучуков, ТЭПа-термоэластопласта, специальных полимерных добавок, СЖК, вследствие чего обладает высокой адгезией, клеящими и гидроизоляционными свойствами, морозостойкостью, прочным сцеплением с бетоном, металлом, деревом.
Сфера применения
Мастика предназначена для антикоррозионной защиты и гидроизоляции бетонных, кирпичных, каменных, металлических, деревянных, и других конструкций в том числе надземных и подземных трубопроводов, металлических труб холодного и горячего водоснабжения и канализации; защита от почвенной коррозии фундаментов, мостовых сооружений, резервуаров различного назначения; битумных и полимерно-битумных поверхностей. Применяется для устройства и ремонта кровли, заделки трещин и швов при кровельных работах. Подходит для качественного приклеивания рулонных материалов и гидроизоляции в местах изгибов и примыканий элементов кровли (трубы, купола, сливы, воронки, ограждения и т.д.), подвижных частей элементов кровли, гидроизоляции бассейнов.
Способ применения
Для получения более качественного гидроизоляционного слоя на пористых, и «слабо держащихся» — мелящихся поверхностях предварительно поверхность обработать битумным или полимерно-битумным праймером производства ООО «ХозДвор».
Перед применением мастику тщательно перемешивают, а затем наносят при помощи шпателя, путем налива с последующим разравниванием. Для нанесения кистью или валиком мастику следует разбавить растворителем в количестве 5-15% от массы мастики сольвентом (нефрасом), толуолом, ксилолом, смесевыми растворителями: 646, 650, 648, 649, Р-4, Р-5 и другими. Для лучшей адгезии может применяться в разогретом состоянии.
Условия нанесения
Температура воздуха и основания при проведении работ должна быть в пределах от -20 до +40°C, относительная влажность воздуха — не более 80%. Основание перед применением должно быть сухим, чистым, прочным, без инея и льда, не содержать веществ, снижающих адгезию. При отрицательной температуре воздуха мастику следует выдержать в теплом помещении одни сутки при температуре не ниже +15°C или подогреть до температуры +30÷50°C, нарушив герметичность тары, вскрыв крышку, при этом запрещается пользоваться открытым огнем. Температура мастики, независимо от температуры воздуха, должна быть не ниже +10°C.
Расход мастики: толщина наносимого слоя не более 1,0мм. Расход 0,8÷1,2кг/м² в зависимости от поверхности. Для формирования наиболее эффективной толщины покрытия и качественной гидроизоляции рекомендуется нанесение 2-3 слоев и прокладыванием между слоями армирующий слой из стеклосетки или стеклоткани. Последующий слой наносится после высыхания предыдущего.
Время высыхания нанесенного слоя при температуре 20°C от 1 до 6 часов в зависимости от влажности воздуха и толщины слоя. Полное высыхание нанесенных слоев 24 часа. При низких температурах время высыхания увеличивается.
Техника безопасности
Мастика содержит органические растворители. При работе с мастикой запрещается курить и пользоваться открытым огнем. Не следует допускать попадания мастики на открытые участки кожи, в глаза и рот. При попадании в глаза необходимо промыть их большим количеством воды и обратиться к врачу. При проведении работ рекомендуется пользоваться защитными очками и перчатками.
Хранение
Хранить в сухом, защищенном от солнечных лучей месте при температуре -25°C до +30°C вдали от отопительных и нагревательных приборов.
Битумная мастика- Производитель битумной мастики- Асфальтовая мастика- RAHA Bitumen Co.
Admin9Рахим Пальто
Мастика битумная
Общее описание мастики битумной
Возведенный с любовью дом, нуждается в защите, и, прежде всего, от влаги. От качества гидроизоляции зависит, какой длины будет фундамент и крыша. Среди многообразия современных материалов есть тот, который обеспечивает бесшовную герметичную защиту от воды даже в труднодоступных местах и на сложных поверхностях по доступной цене – это 9Асфальтовая мастика 0011.
В настоящее время асфальтобетонная мастика – это «коктейль» из природного битума (один из продуктов нефтепереработки) и синтетических компонентов модификатора для увеличения срока службы покрытия, сцепления и удобства нанесения. Он подходит не только для гидроизоляции поверхностей из кирпича, бетона и дерева, но и для шпаклевки неровностей, заполнения трещин, приклеивания кровельных мембран. Мастика имеет очевидные преимущества, такие как высокая эластичность, способность долго держаться практически на всех поверхностях, трещинах и изломах, стойкость к агрессивным средам.
- Позиция добавки. Основные группы: битумная мастика – традиционный недорогой материал,
- мастика битумная – покрытие с повышенной эластичностью и устойчивостью к внешним воздействиям,
- Мастика битумная Эмульсионная – предназначена для предварительной обработки поверхностей перед гидроизоляцией, также называемая «грунтовкой» (о них можно прочитать здесь) более жидкой консистенции,
- Мастика битумная -полимерная – составы с добавлением синтетического каучука, пластификаторов, растворителей, повышающие срок службы и качество покрытия.
Кроме того, битумная мастика известна и используется в течение многих лет в качестве атмосферостойкого и изнашиваемого покрытия для крыш, полов, пешеходных дорожек и светлых подъездных путей. Он состоит в основном из градуированного минерального заполнителя и битумного вяжущего и отличается от битумного изнашиваемого покрытия улиц и дорог тем, что содержит такое количество битумного вяжущего, что в горячем состоянии имеет консистенцию теста, так что его можно сжимать и уплотнять. сгладить до истинной поверхности легкими ручными инструментами, такими как деревянная терка или шпатель. С другой стороны, битумная изнашиваемая поверхность улиц и проезжих частей относительно бедна битумным связующим и даже в горячем состоянии все еще имеет зернистый и относительно сухой вид и состояние.
Битумная мастика производится под руководством высококвалифицированных специалистов с использованием растворителя высшего сорта и других сырьевых компонентов в соответствии с заранее определенными отраслевыми стандартами. Он также известен как резиновый мастичный герметик для швов на основе растворителя и широко используется в качестве герметика для бетона, кирпичной кладки и других строительных материалов.
Предлагаемая битумная мастика известна своей жесткой и эластичной герметизирующей природой, а также высокой устойчивостью к истиранию и температуре. Мы обеспечиваем это в различных количествах и экономичных ставках для наших уважаемых клиентов.
Мастика битумная герметизирующая
Мастика битумная герметизирующая может использоваться в широком диапазоне применений, например: заделка трещин, порезов и пузырей, которые могут возникнуть на гидроизоляционном слое; для герметизации деталей (сливов, вентиляционных отверстий, дренажных труб, дымоходов, углов и т.д.), для усиления стыков и слабых мест битумной мембраны, герметизации механических креплений и фиксации битумной черепицы. Bitumen Sealing Mastic — это битумная мастика, специально разработанная для использования вместе с полимерно-битумной мембраной ITLS P+V для герметизации таких участков кровли, как детали, периметры, выступающие объекты и т. д.
Bitumen Sealing Mastic представляет собой гибкую битумную мастику, армированную синтетическими волокнами, которая после высыхания образует пластифицированный слой с превосходной адгезией. БИТУМНАЯ МАСТИКА обладает отличной адгезией и долговечностью на битумных поверхностях, оцинкованных листах, гладких и волнистых металлических листах, бетоне, фиброцементе и т.д., которая остается неизменной во времени. Продукт обладает отличной стойкостью к старению, УФ-излучению. лучевой и атмосферной агрессии. Мастика Bitumen Sealing Mastic также может наноситься при температуре ниже 0 °C на слегка влажные поверхности и совместима со всеми типами битумных мембран.
Нанесение битумной мастики
БИТУМНАЯ МАСТИКА представляет собой пластичный, нетекучий состав, обеспечивающий эффективное уплотнение между большинством кровельных материалов. Используется для общего гидроизоляционного и герметизирующего ремонта; заделка трещин, отверстий и стыков в качестве отделки или перед нанесением других материалов, а также для ремонтных работ перед нанесением SEALOFLASH или ALLPRUFE.
Заполнение трещин и щелей – в бетоне, толе, асфальте, свинце, цинке, гофрированном асбестоцементе, стали, кирпичной кладке и штукатурке.
Герметизация швов в желобах, желобах, водосточных трубах, между гофрированными асбестоцементными и железными листами, вокруг фонарей и сборных железобетонных элементов.
Постельные плитки, сланцы и оклады на месте.
Битумная мастика устойчива к кислотам и щелочам для использования в качестве защитной непроницаемой мембраны, подходящей для бетона, кирпичной кладки, стали и т. д.
Битумная мастика обладает хорошей устойчивостью к большому количеству умеренно коррозионных условий.
Асфальтовая мастика, Битум, Битумная мастика, Битумная мастика для полов, Битумно-мастичная мастика, купить битумную мастику, эластомерная битумная мастика горячего нанесения, Иран Асфальтовая мастика, Иран Асфальтовая мастика Производитель, Иран Битумная мастика, Иран Битумная мастика Производитель, Поставщик битумной мастики в Иране, эластомерный битум в Иране, производитель эластомерного битума в Иране, эластомерная битумная мастика горячего нанесения в Иране, битумная мастика Ирана, битум, модифицированный полимером Ирана, битумная мастика, битумная мастика, ремонт любого мостового соединения, ремонт любого мостового соединения эластомерным горячим битумом мастика
2 июля 2018 г.
Оценка способности битумных мастик к самовосстановлению
Оценка способности битумных мастик к самовосстановлению
Скачать PDF
Скачать PDF
- Открытый доступ
- Опубликовано:
- J. Qiu 1,2 ,
- M. van de ven 1 ,
- S. wu 2 ,
- J. Yu 2 и
- …
- . A. 2 и
- …
- .
. A. и
- …
- .. A. и
- …
- .A. и
- …
- A. A. и
- …
- .A. .
Экспериментальная механика том 52 , страницы 1163–1171 (2012)Процитировать эту статью
3493 Доступ
58 цитирований
Сведения о показателях
Abstract
Способность битумных материалов к самовосстановлению известна уже много лет. Исследования в основном были сосредоточены на самовосстановлении поведения во время повторений нагрузки. Тесты требуют много времени и/или сложны. В этой статье представлена простая процедура теста на самовосстановление, сочетающая тест «заживление-повторный перелом» (FHR) с морфологическими наблюдениями. Сначала была применена нагрузка с высокой скоростью смещения, чтобы образовалась плоская открытая трещина шириной 100–200 мкм. Затем образец помещали в форму из силиконовой резины для заживления. Были применены различные периоды заживления, температуры и модификации материалов. Флуоресцентную микроскопию использовали для наблюдения за морфологическими изменениями в периоды заживления. После заживления образец подвергали повторному разрушению в тех же условиях, что и исходное испытание на разрушение. Экспериментальные результаты показывают, что способность к самовосстановлению, количественно определяемая прочностью на повторный излом, увеличивается с увеличением времени заживления и повышением температуры заживления.
Основная кривая восстановления прочности при любой температуре заживления может быть получена с помощью принципа суперпозиции время-температура. При сравнении основной кривой восстановления прочности с наблюдениями за морфологическим заживлением с помощью флуоресцентной микроскопии можно предположить, что процесс заживления, наблюдаемый в этой статье, представляет собой процесс, управляемый вязкостью, состоящий из двух этапов, а именно закрытия трещины и увеличения прочности. Битумная мастика, модифицированная стирол-бутадиен-стирольным полимером, демонстрирует более низкую способность к заживлению, чем стандартная битумная мастика со степенью проникновения 70/100. Процедура испытаний, предложенная в этой статье, оказалась простой и эффективной для оценки и сравнения способности битумных материалов к самовосстановлению.
Введение
Способность битумных материалов к самовосстановлению известна уже много лет [1, 2]. Были проведены различные исследования исцеления, чтобы квалифицировать и количественно оценить это явление. Известно, что способность к самовосстановлению представляет собой довольно сложное явление, которое зависит от различных факторов, включая время заживления, температуру заживления, фазы трещин, модификации материала и локализацию. Были разработаны различные подходы, такие как испытание на прерывистую усталость с различным соотношением периодов отдыха и периода нагрузки [3], испытание на усталость-заживление-переутомление [4, 5], внутреннее испытание на заживление из двух частей [6, 7] и перелом включал тест на заживление [8, 9]. За подробностями этих подходов читатель может обратиться к обзору литературы, сделанному Qiu [10]. В большинстве случаев способность к самовосстановлению исследуется с помощью теста на усталость с периодами отдыха для восстановления, что очень сложно и требует много времени. Следовательно, необходимо оценить способность к самовосстановлению простым и эффективным способом.
Хаммум и Миллард разработали простой тест на повторное локальное разрушение для изучения свойств самовосстановления чистого битума [8, 11]. Битумное вяжущее удерживалось между двумя полусферическими выступами, имитирующими два заполнителя в асфальтовой смеси. Все испытания проводились при 0°С. К системе применялась растягивающая нагрузка, регулируемая смещением, со скоростью смещения 12,5 мкм/с в течение 4 с. После загрузки система возвращалась к исходной толщине зазора между сферами. Затем проводили залечивание возможных трещин с интервалами времени залечивания 2 мин и 2 ч. В период заживления к держателю образца прикладывалась небольшая сжимающая нагрузка 50 Н. После периода заживления снова применялась нагрузка. После 2 часового заживления битум мог почти восстановить свои первоначальные свойства разрушения в отношении нагрузки и кривой повторного нагружения.
Авторы этой статьи провели исследования способности к самовосстановлению различных типов битума с помощью испытания на прямое растяжение (DTT) [9]. Образец битума прямого натяжения в форме собачьей кости, изготовленный из формы из силиконовой резины, разрезали на две равные части острым ножом при 5°С. Затем две срезанные поверхности приводили в контакт друг с другом, помещали в форму из силиконового каучука и хранили при комнатной температуре (около 22°C) в течение 3, 6, 20 и 48 часов. После периода заживления прочность определяли в тесте DTT при 0°C при скорости перемещения 10 мм/мин. Было показано, что после 6 часовых периодов заживления при комнатной температуре прочность восстанавливалась до значения исходного неповрежденного образца.
Таким образом, процедура испытаний на заживление трещин, связанных с трещинами, кажется многообещающей для исследования способности битумных материалов к самовосстановлению простым и эффективным способом. Однако методы, предложенные в литературе, были слишком эмпирическими. Ни один из методов испытаний не дает четкой информации о ситуации с трещиной, что считается важным для количественной оценки способности к самовосстановлению. Чтобы описать ситуацию с трещинами, к процедуре перелом-заживление-повторный перелом (FHR) было добавлено наблюдение под микроскопом. Полезность этой новой процедуры для оценки способности битумной мастики к самовосстановлению будет описана в этой статье.
Экспериментальный
Материалы
В этом исследовании использовались два типа битумных вяжущих:
Стандартный битум Kuwait Petroleum класса пенетрации 70/100 с пенетрацией 93 (0,1 мм) при 25°C и температурой размягчения 45°C;
Битум, модифицированный полимером стирол-бутадиен-стирол (СБС) от Shell, с пенетрацией 65 (0,1 мм) при 25°C и температурой размягчения 70°C [12].
Мастики битумные получены путем смешивания битумных вяжущих с известняковым наполнителем Wigro в массовом соотношении 1:1. В данной работе мастика с битумной пенетрацией 70/100 называется ПБмас, а битум, модифицированный полимером СБС, называется СБСмас. Опорные кривые комплексного модуля и фазового угла ПБмас и ВРМс при эталонной температуре 0°C показаны на рис. 1.
Изображение полного размера
Процедура испытаний
Испытания FHR проводились с использованием машины для испытаний на прямое растяжение (ATS 900DTTS) с температурной камерой. Процедура эксперимента обсуждается ниже, а также показана на рис. 2:
Рис. 2Иллюстрация процедуры испытания FHR
Полноразмерное изображение
Подготовка. Перед испытанием FHR образцы были изготовлены в предварительно нагретой силиконовой резиновой форме и покрыты другим куском предварительно нагретой силиконовой резины, чтобы получить одинаковую текстуру с каждой стороны образца и избежать температурного воздействия на образцы [13]. После охлаждения в холодильнике образцы извлекали из формы и помещали в термокамеру машины ДТТ не менее чем на 2 ч при 0°С.
Перелом.
Исходные образцы разрушали со скоростью перемещения 100 мм/мин при 0°C.
Исцеление. Две сломанные части образца были помещены обратно в форму из силиконовой резины для заживления. Из-за ограниченной деформации образца после разрушения две сломанные части хорошо вписываются в форму с видимой трещиной, как показано на рис. 3. Различные температуры восстановления 10 ° C, 20 ° C и 40 ° C и восстановление периоды 3 ч, 6 ч и 24 ч применялись как для PBmas, так и для SBSmas.
Рис. 3Иллюстрация размещения двух сломанных деталей ( слева ) в форме из силиконовой резины ( справа )
Изображение в полном размере
Микроскопическое наблюдение. Флуоресцентную микроскопию Olympus также использовали для исследования морфологических изменений образца в течение периода заживления при температуре окружающей среды (около 25°C).
Время наблюдения составляло 0, 1, 3, 8 и 18 ч.
Повторный перелом. После периодов заживления образцы снова кондиционировали до 0°C в течение не менее 2 ч, а затем извлекали из формы. После этого образцы подвергали повторному разрушению со скоростью перемещения 100 мм/мин при 0°C.
Процент самовосстановления был рассчитан путем деления прочности на излом залеченного образца на прочность на излом исходного образца: 9где ,
- Г:
— процент самовосстановления
- S преломление :
— прочность повторно разрушенных образцов
- S перелом :
– прочность исходных разрушенных образцов.
Результаты и обсуждение
Геометрия образца
Перед испытанием FHR особое внимание уделялось геометрии образца. Предыдущие тесты на заживление проводились со стандартным образцом DTT [9]. Однако было показано, что образцы DTT не подходят для исследований самовосстановления по следующим причинам. Во-первых, внезапный разрыв обычных образцов DTT во время испытания на разрушение может привести к тому, что образец расколется более чем на две части, что сделает дальнейшее заживление и повторное разрушение невозможным. Во-вторых, чтобы получить представление о заживлении трещины, предполагалось, что поверхность повторного разрушения должна быть такой же, как и поверхность разрушения. Однако иногда повторно разрушенный образец ломался не в том месте, где была первая поверхность разрушения, что приводило к различным результатам. Следовательно, существует потребность в специальной геометрии образца для исследований самовосстановления.
Как показано на рис. 4, на основе испытаний на разрушение, основанных на механике разрушения, описанных в литературе [14–16], образцы были разработаны с формой сосредоточенного напряжения. Были разработаны два типа образцов с концентрированным напряжением, а именно образец с двойной кромкой с надрезом (DN) и образец с двойной кромкой параболической формы (DP). Для сравнения использовали стандартный образец DTT в форме собачьей кости.
Рис. 4Иллюстрация специальной геометрии образцов (от сверху до снизу : DTT, DN, DP)
Изображение в полный размер
На рисунке 5 показан коэффициент концентрации напряжений в разработанных образцах с помощью моделирования методом конечных элементов [17]. Для простоты модуль упругости 50 МПа и коэффициент упругости 0,45 были произвольно выбраны и присвоены битумным мастикам. Была приложена растягивающая нагрузка 100 Н. Хорошо видна концентрация напряжений в середине образцов DN и DP. Однако для стандартной геометрии образца ДТТ распределение напряжений в средней части практически постоянно, что не позволяет предсказать предел прочности. Это также может объяснить, почему стандартный образец DTT может расколоться более чем на две части при испытании на разрушение.
ABAQUS моделирование геометрии специальных образцов (от вверху до внизу : DTT, DN, DP)
Изображение в полный размер
в качестве условия испытания на разрушение была выбрана температура 0°C. На рисунке 6 показаны кривые разрушения различной геометрии для скорости перемещения 100 мм/мин при температуре 0°C. Образец DN и образец DP демонстрируют одинаковое поведение при разрушении. Однако на практике извлечение образца DN из формы из силиконового каучука очень затруднено. Из-за высокой концентрации напряжения в надрезе его можно легко повредить во время извлечения из формы. В то время как образец DP показал гораздо лучшую работоспособность.
Результаты испытаний образцов ПБмас различной геометрии при скорости перемещения 100 мм/мин при температуре 0°С
Изображение в полный размер
На рис. скорости сравниваются. Образец внезапно ломается посередине со скоростью перемещения 100 мм/мин из-за концентрации напряжений. Однако образец, который был испытан при скорости перемещения 10 мм/мин, показывает трещины в форме аллигатора в середине образца. Микротрещины и макротрещины инициируются и распространяются по всему образцу вместо внезапного разрыва.
Рис. 7Иллюстрация поверхности излома образцов после нагрузки 100 мм/мин ( слева ) и 10 мм/мин ( справа )
Изображение в полный размер
В результате образец ДП с скорость смещения 100 мм/мин при температуре 0°C использовалась в тесте FHR.
Восстановление силы
На рисунке 8 показаны результаты теста FHR для PBmas и SBSmas. Так как битумные материалы имеют температурно-временную зависимость, такая же особенность может наблюдаться и в процессе самовосстановления. Процент заживления увеличивается с увеличением времени заживления и повышением температуры заживления. При сравнении скорости заживления PBmas и SBSmas можно сделать следующие наблюдения. Процент заживления как PBmas, так и SBSmas составляет всего 10% после заживления при 10°C. PBmas демонстрирует более быстрое заживление при температуре 20 ° C и 40 ° C, которое приближается почти к 80% после периода заживления в течение 24 часов. SBSmas демонстрирует ограниченную способность к заживлению при 20°C, но высокую скорость заживления при 40°C.
Результаты испытаний на самовосстановление PBmas и SBSmas
Изображение в полный размер
Для моделирования температурно-временной зависимости процесса самовосстановления была построена основная кривая восстановления прочности с использованием суперпозиции время-температура принцип. Использовали S-образное уравнение, как показано в уравнении (2), которое было похоже на модель Кристенсена-Андерсона для основных кривых комплексного модуля битумных вяжущих [18, 19]. Коэффициент сдвига суперпозиции время-температура в уравнении (3) основан на уравнении Аррениуса. 9{\frac{n}{{\log 2}}}} $$
(2)
$$ \log {\alpha_T}(T) = \frac{{\Delta {E_a}}}{{2,303 R}}\left( {\frac{1}{T} — \frac{1}{{{T_0}}}} \right) $$
(3)
Где:
- \( {\alpha_T} \) :
— коэффициент сдвига суперпозиции время-температура
- м, н:
— параметры модели
- Δ Е и :
– кажущаяся энергия активации, Дж/моль
- Р:
— универсальная газовая постоянная, 8,314 Дж /( моль · К ).
На рис. 9 показаны основные кривые восстановления прочности как для PBmas, так и для SBSmas при эталонной температуре 20 °C. Соответствующие параметры модели показаны в таблице 1. Показано, что PBmas может приблизиться к 100% заживлению за гораздо меньшее время, чем SBSmas.
Рис. 9Основные кривые самовосстановления сопротивления повторному разрушению битумных мастик при эталонной температуре 20°C0003
Морфологическое наблюдение
На рисунке 10 показано поперечное сечение PBmas и SBSmas после перелома. SBSmas имеет четко блестящие пятна на поперечном сечении по сравнению с PBmas, которые, как полагают, представляют собой разорванные молекулы SBS. Согласно статистическому анализу фотографии, молекулы SBS покрывают около 25% площади поверхности.
Рис. 10Флуоресцентная микроскопия поперечного сечения PBmas ( слева ) и SBSmas ( справа )
Полноразмерное изображение
На рисунке 11 представлены морфологические измерения PBmas в разное время заживления. Размер трещины составляет около 150 мкм, и закрытие трещины можно четко отслеживать с течением времени. После периода заживления 3 ч трещина исчезает из-за полного закрытия трещины.
Флуоресцентная микроскопия образца PBmas с разным временем заживления (0, 1, 3 и 18 ч)
Полноразмерное изображение
На рисунке 12 показано морфологическое измерение в процессе заживления SBSmas. Первоначально трещина составляет около 100 мкм. Интересно видеть, что скорость закрытия трещины намного меньше по сравнению с образцом PBmas. Через 8 часов после заживления трещину все еще можно наблюдать.
Рис. 12Флуоресцентная микроскопия образца SBSmas с разным временем заживления (0, 3 и 8 ч)
Изображение в натуральную величину . На рис. 13 можно наблюдать две фазы, а именно закрытие трещины и увеличение прочности. Замечено, что полное закрытие трещины не означает полного восстановления сопротивления повторному разрушению. После того, как трещина закрыта, битумные образцы все еще могут иметь микротрещины и пузырьки воздуха внутри образца, которые нелегко обнаружить. Для набора прочности образца все еще требуется дополнительное время заживления. Следовательно, природа битумного вяжущего оказывает огромное влияние на процесс заживления. Считается, что заживление в этой фазе трещины зависит от вязкости [13].
Сравнение процесса закрытия трещины и процесса восстановления прочности при температуре 25°C
Изображение в натуральную величину
демонстрирует превосходную способность к заживлению как на этапе закрытия трещины, так и на этапе набора прочности. Модификация полимера СБС дает значительное улучшение высокотемпературных и низкотемпературных свойств битумных вяжущих за счет полимерной сетки. Однако сеть также поглощает мягкие компоненты из битума, в результате чего получается битум с высокой вязкостью. Это может быть причиной того, что SBSmas показывает более низкую скорость заживления. Кроме того, как известно, молекулы СБС стабильны при температурах испытаний от 10°С до 40°С, а это означает, что при этих температурах не будет происходить никаких фазовых переходов или физико-химических реакций. Таким образом, разрушенные молекулы SBS не могут восстанавливаться в процессе заживления и будут действовать как «наполнитель» в битумной системе. Более того, разорванные молекулы СБС создают трудности для смачивания и взаимной диффузии в процессе заживления. Но это влияние меньше при более высокой температуре. Все эти причины в сумме приводят к более низкой скорости заживления SBSmas.
Выводы и рекомендации
Способность битумных мастик к самовосстановлению была исследована с помощью микроскопической процедуры испытаний на заживление-повторное разрушение. На основании данных испытаний и анализа можно сделать следующие выводы:
- а.
Доказано, что процедура испытаний способна оценить способность к самозаживлению открытой трещины простым и эффективным способом.
- б.
Основная кривая восстановления прочности может быть получена с использованием принципа суперпозиции время-температура.
- в.
Считается, что заживление открытой трещины зависит от вязкости. Процесс заживления включает две фазы: закрытие трещины и увеличение прочности. Завершение процесса закрытия трещины не означает полного восстановления прочности.
- д.
Отрицательное влияние модификации полимера на способность к самовосстановлению можно наблюдать отчетливо. Битумная мастика, модифицированная СБС, демонстрирует более низкую способность к самовосстановлению, чем стандартная битумная мастика с пенетрацией 70/100, как в фазе закрытия трещин, так и в фазе набора прочности.
В будущем исследования будут направлены на дальнейшее внедрение простой процедуры испытаний для разработки новых самовосстанавливающихся компонентов и сравнение возможностей самовосстановления различных типов битумных материалов. Кроме того, вместо оценки внутренней способности битумных материалов к самовосстановлению эта простая процедура испытаний также может быть применена для оценки способности герметиков и материалов для швов герметизировать трещины.
Каталожные номера
Van Dijk W, Moreaud H, Quedeville A, Uge P (1972) Усталость битума и битумных смесей. Документ, представленный на 3-й международной конференции. Конференция по структурному проектированию асфальтовых покрытий, Анн-Арбор, Мичиган, США
Франкен Л. (1979) Усталостные характеристики битумной дорожной смеси в реалистичных наилучших условиях.
Transp Res Rec 712:30–34
Google Scholar
Shen S, Chiu H-M, Huang H (2010) Характеристика усталости и заживления асфальтовых вяжущих. J Mater Civ Eng 22 (9):6
Артикул Google Scholar
Phillips MC (1998) Многоступенчатые модели усталости и заживления, а также свойства вяжущего, участвующие в заживлении. Доклад, представленный на семинаре Eurobitume по эксплуатационным свойствам битумных вяжущих, Люксембург
Шан Л., Тан Ю., Андервуд С., Ким Ю.Р. (2010) Применение тиксотропии для анализа характеристик усталости и заживления асфальтового вяжущего. Документ, представленный на ежегодном собрании Совета по исследованиям в области транспорта 2010 г.
Бхасин А., Литтл Д.Н., Боммаварам Р., Васконселос К. (2008) Схема количественной оценки эффекта заживления битумных материалов с использованием свойств материалов.
Road Mater Pavement Des EATA2008:219–242
Google Scholar
Qiu J, van de Ven MFC, Wu SP, Yu JY, Molenaar AAA (2011) Изучение поведения чистого битума при самовосстановлении с использованием динамического сдвигового реометра. Топливо 90(8):2710–2720
Артикул Google Scholar
Hammoum F, de La Roche C, Piau JM (2002) Экспериментальное исследование разрушения и заживления битума при псевдоконтакте двух заполнителей. Документ, представленный на 9-й Международной конференции по асфальтовым покрытиям
Цю Дж., Ван де Вен MFC, Ву С.П., Ю Дж.И., Моленаар ААА (2009 г.) Исследование способности битумных вяжущих к самовосстановлению. Road Mater Pavement Des 10(SI):81–94
Артикул Google Scholar
Qiu J (2008) Самовосстановление асфальтовых смесей: обзор литературы.
Отчет 7-08-183-1. Делфтский технологический университет, Делфт
Google Scholar
Maillard S, De La Roche C, Hammoum F, Gaillet L,such C (2004) Экспериментальное исследование разрушения и заживления битума при псевдоконтакте двух заполнителей. Доклад, представленный на 3-м конгрессе Eurasphalt & Eurobitume, Вена
SHELL (2003) Productinformatie 1539NL01 Карифальт XS. Shell Nederland Verkoopmaatschappij B.V.
Muraya PM (2007) Остаточная деформация асфальтовых смесей. Делфтский технологический университет
Erkens SMJG (2002) Реакция асфальтобетона (ACRe) – определение, моделирование и прогнозирование. Технологический университет Делфта
Hesp SAM (2004 г.) Усовершенствованный метод спецификации низкотемпературного битумного вяжущего. Заключительный отчет, Контракт MTO № 9015-A-000190 и Контракт NCHRP-IDEA № 84.
Кингстон, Онтарио
Hesp SAM (2006 г.) Разработка улучшенного подхода к тестированию спецификаций битумного вяжущего. Заключительный отчет по проекту Highway IDEA Project 104. Кингстон, Онтарио
ABAQUS (2006 г.) Руководство пользователя ABAQUS, версия 6.6.
Christensen DW, Anderson DA (1992) Интерпретация данных динамических механических испытаний асфальтобетонных материалов для дорожного покрытия. J Assoc Asph Paving Technol 61:67–116
Google Scholar
Волдекидан М., Хуурман М., Мо Л. (2010) Испытания и моделирование реакции битумного раствора. J Wuhan Univ Technol — Mater Sci Ed 25 (4): 637–640. дои: 10.1007/s11595-010-0060-9
Артикул Google Scholar
Скачать ссылки
Благодарность
Первый автор хотел бы поблагодарить Китайский стипендиальный совет за финансовую помощь. Авторы высоко оценивают сотрудничество между Уханьским технологическим университетом и Делфтским технологическим университетом и выражают желание продлить и укрепить текущее сотрудничество между упомянутыми технологическими институтами. Обсуждения и предложения, сделанные д-ром Лиантонгом Мо и г-ном Ад Пронк, были высоко оценены. Авторы также благодарят рецензентов за ценные обсуждения и предложения.
Открытый доступ
Эта статья распространяется в соответствии с условиями некоммерческой лицензии Creative Commons Attribution, которая разрешает любое некоммерческое использование, распространение и воспроизведение на любом носителе при условии указания автора(ов) и источника.
Информация об авторе
Авторы и организации
Дорожное и железнодорожное строительство, Факультет гражданского строительства и наук о Земле, Делфтский технологический университет, 2600GA, Делфт, Нидерланды
Дж. Цю, М. ван де Вен и А. Моленаар
Ключевая лаборатория технологии силикатных материалов Министерства образования, Уханьский технологический университет, Ухань, 430070, Китай
Дж.
Цю, С. Ву & J. Yu
Авторы
- J. Qiu
Просмотр публикаций автора
Вы также можете искать этого автора в PubMed Google Scholar
- M. van de Ven
Посмотреть публикации автора
Вы также можете искать этого автора в PubMed Google Scholar
- S. Wu
Просмотр публикаций автора
Вы также можете искать этого автора в PubMed Google Scholar
- J. Yu
Просмотр публикаций автора
Вы также можете искать этого автора в PubMed Google Scholar
- A. Molenaar
Просмотр публикаций автора
Вы также можете искать этого автора в PubMed Google Академия
Автор, ответственный за переписку
Дж. Цю.
Права и разрешения
Открытый доступ Это статья в открытом доступе, распространяемая в соответствии с условиями некоммерческой лицензии Creative Commons Attribution (https://creativecommons.